Our Services
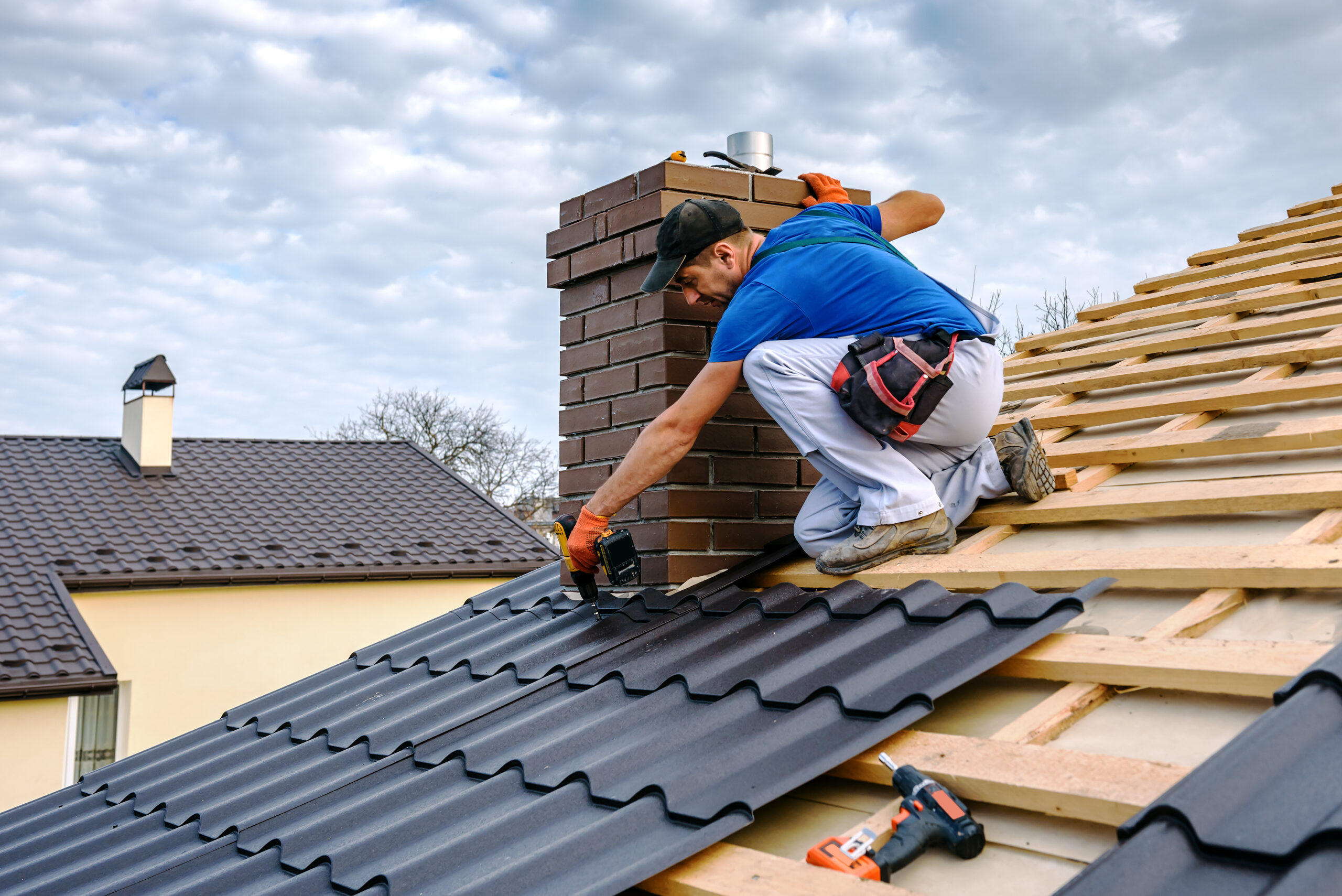
The Process of Sweeping:
- Inspection: Before sweeping, a professional chimney sweep will inspect the chimney to identify any major obstructions or damage.
- Sweeping: Using specialized brushes and rods, the sweep will clean the flue from the top down or bottom up, depending on access points.
- Final Check: After sweeping, a final inspection ensures that the chimney is clean and free of obstructions.
Sweeping
Chimney sweeping is a fundamental service essential for maintaining a safe and efficient fireplace or wood-burning stove. Over time, the use of fireplaces leads to the accumulation of soot, creosote, and debris inside the chimney. These deposits can reduce airflow, leading to inefficient burning and potentially hazardous conditions, including chimney fires.
Why Sweeping is Important:
- Prevention of Chimney Fires: Creosote, a byproduct of burning wood, is highly flammable. A significant buildup can ignite, causing dangerous chimney fires.
- Improved Airflow: Regular sweeping ensures that the chimney is clear of obstructions, allowing smoke and gases to escape efficiently.
- Prolonged Chimney Life: Removing corrosive deposits regularly helps prevent deterioration of the chimney structure.
Chemical Cleaning
In addition to mechanical sweeping, chemical cleaning is sometimes necessary to remove stubborn creosote deposits. This method involves applying chemicals that break down creosote, making it easier to remove.
When to Use Chemical Cleaning:
- Heavy Creosote Buildup: In cases where creosote has hardened into a glaze, chemical cleaning is more effective than traditional sweeping.
- Regular Maintenance: Chemical treatments can be part of regular maintenance, especially for chimneys that experience heavy use.
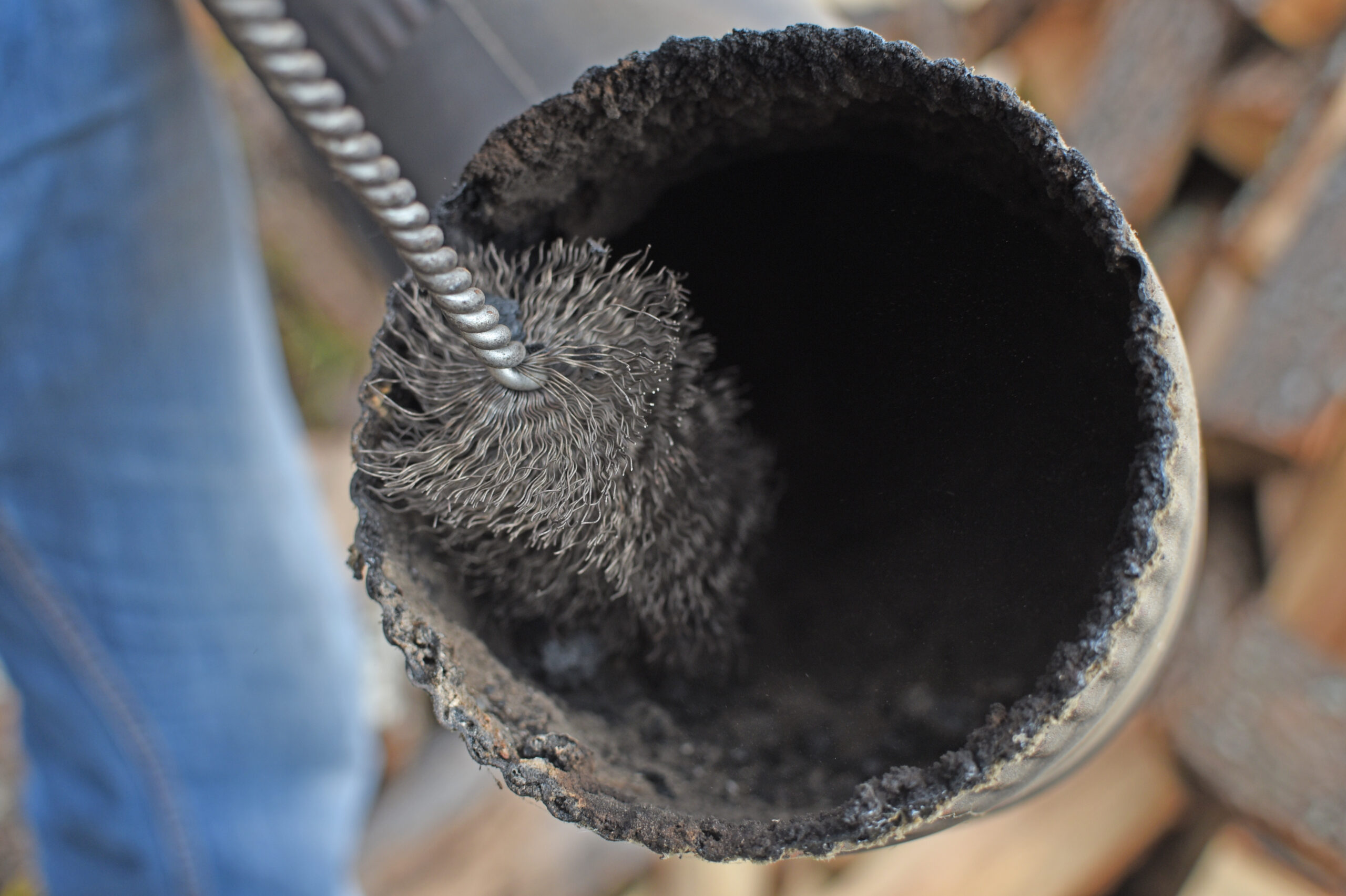
The Chemical Cleaning Process:
- Application: A chemical agent is applied to the creosote-covered areas of the chimney.
- Soaking Period: The chemicals are left to soak, breaking down the creosote over a specified period.
- Removal: After the chemicals have worked, the loosened creosote is swept out using traditional methods.
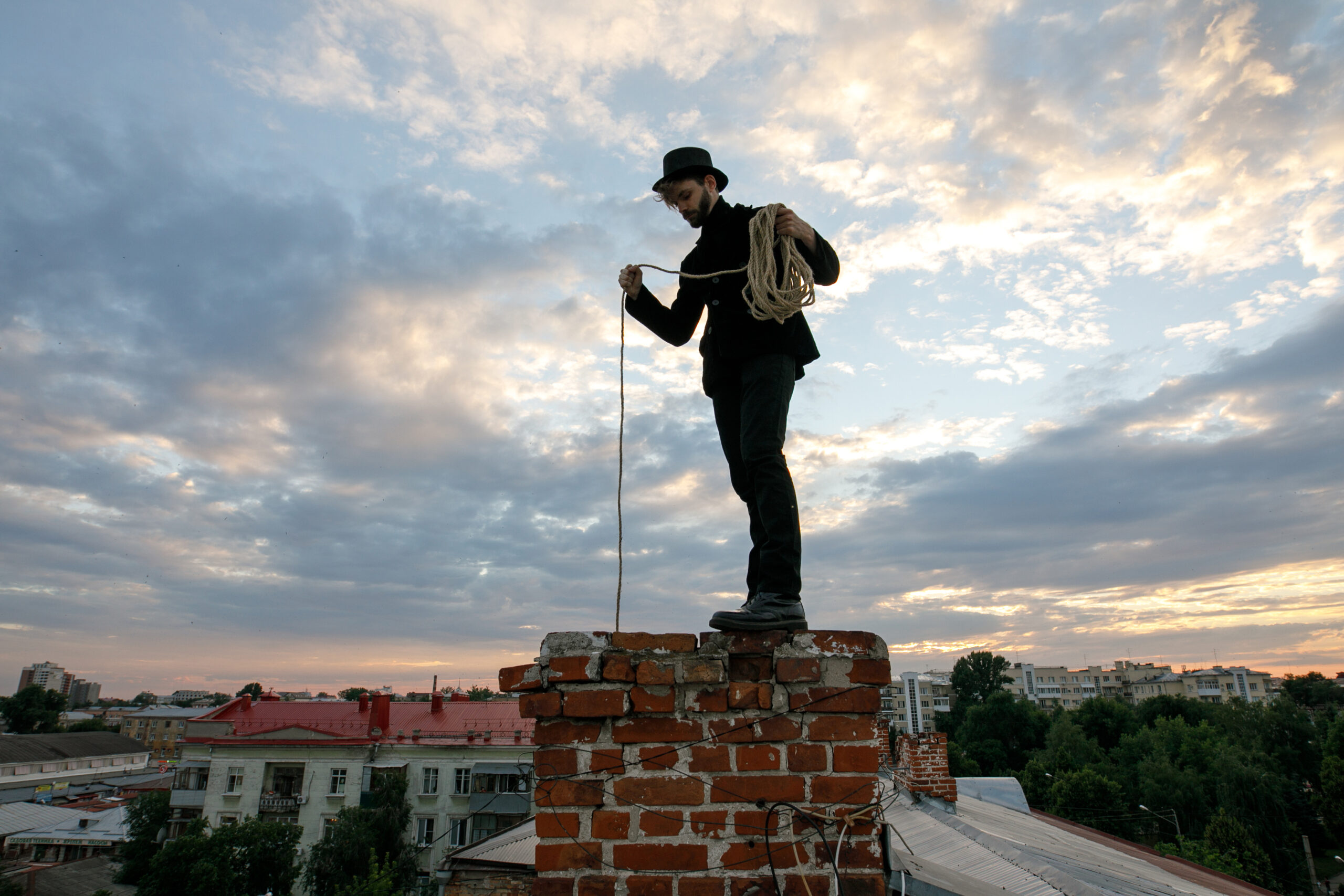
Solutions to Smoke Problems:
- Clearing Obstructions: Regular sweeping can prevent blockages that lead to smoke problems.
- Installing a Chimney Cap: A cap can prevent debris from entering the chimney and also help with airflow.
- Flue Lining: Ensuring that the flue is properly lined and sized for the fireplace is crucial.
Smoke Problems
Smoke problems can arise from various issues within the chimney system, leading to smoke backing up into the home. This can be both a nuisance and a health hazard.
Common Causes of Smoke Problems:
- Blockages: Obstructions like bird nests, leaves, or creosote buildup can restrict airflow.
- Improperly Sized Flue: If the flue is too small for the fireplace, it may not be able to handle the volume of smoke.
- Air Pressure Issues: Negative air pressure in the home can cause smoke to be pulled back down the chimney.
- Cracks in the Chimney: Cracks or leaks in the chimney can cause smoke to escape into other parts of the house.
Chimney Leaks
Water intrusion is a common problem for chimneys, leading to a range of issues from minor leaks to significant structural damage.
Causes of Chimney Leaks:
- Cracked or Damaged Masonry: Water can enter through cracks in the chimney’s bricks or mortar.
- Faulty Flashing: Flashing around the chimney may deteriorate over time, allowing water to seep in where the chimney meets the roof.
- Damaged Chimney Cap: A broken or missing cap can allow rainwater to enter the chimney directly.
- Spalling Bricks: Water absorption can cause the outer layer of bricks to flake off, known as spalling.
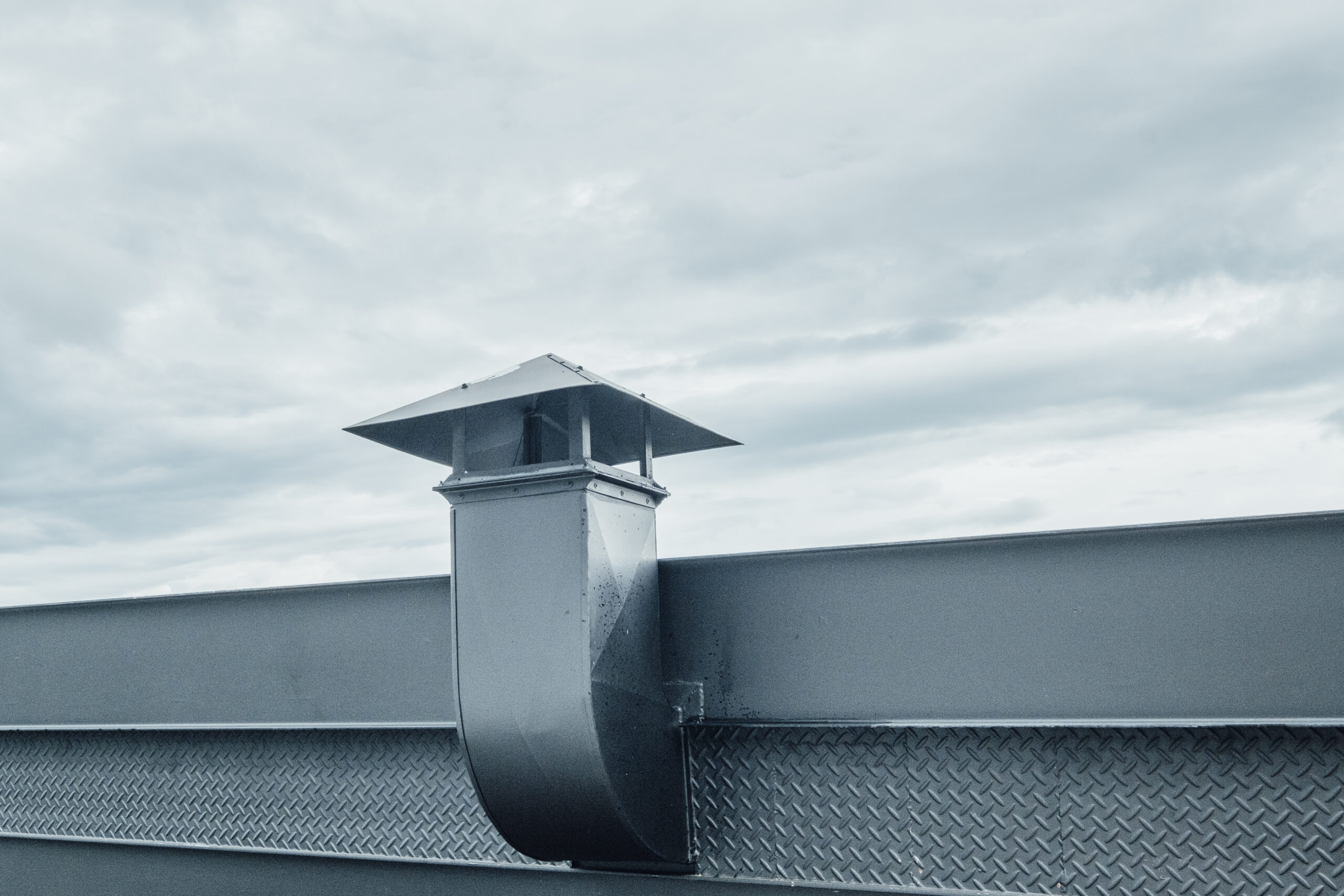
Addressing Chimney Leaks:
- Masonry Repairs: Tuckpointing or rebuilding can address cracks and spalling.
- Flashing Repairs: Replacing or repairing the flashing can prevent water from entering around the chimney base.
- Chimney Cap Installation: Installing or replacing a chimney cap keeps water out of the flue.
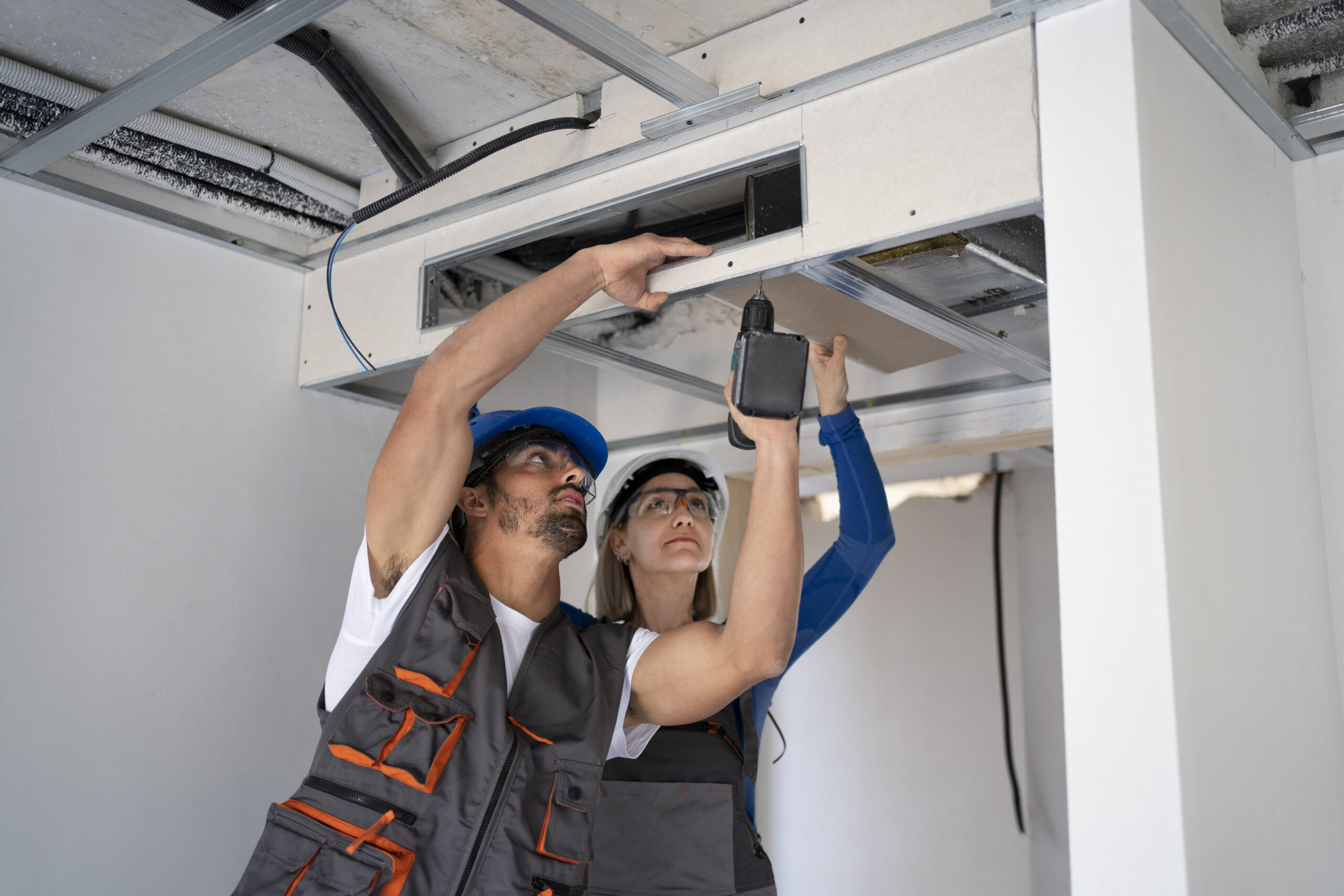
Repair Solutions:
- Reparging: Applying a new layer of mortar can smooth out the smoke chamber and improve draft.
- Sealing Cracks: Cracks in the smoke chamber can be sealed with refractory mortar to prevent leaks.
- Reshaping: In some cases, the smoke chamber may need to be reshaped or resized to improve performance.
Smoke Chamber Repair
The smoke chamber is the area just above the fireplace that funnels smoke into the flue. A well-functioning smoke chamber is essential for proper drafting.
Common Smoke Chamber Issues:
- Cracks: Cracks in the smoke chamber can allow smoke and gases to escape into the home.
- Parge Coating: Many smoke chambers are coated with a layer of mortar (parging) to smooth out rough surfaces. Over time, this coating can deteriorate.
- Improper Design: If the smoke chamber is not built to the correct proportions, it can cause drafting issues.
Chimney Pointing
Chimney pointing involves repairing the mortar joints between bricks or stones in a chimney. Over time, the mortar can deteriorate, leading to structural instability and water leaks.
Why Pointing is Important:
- Preventing Water Ingress: Damaged mortar can allow water to seep into the chimney, leading to leaks and internal damage.
- Structural Integrity: Repointing restores the strength of the chimney structure, preventing collapse or further damage.
- Aesthetic Appeal: Freshly pointed mortar enhances the appearance of the chimney.
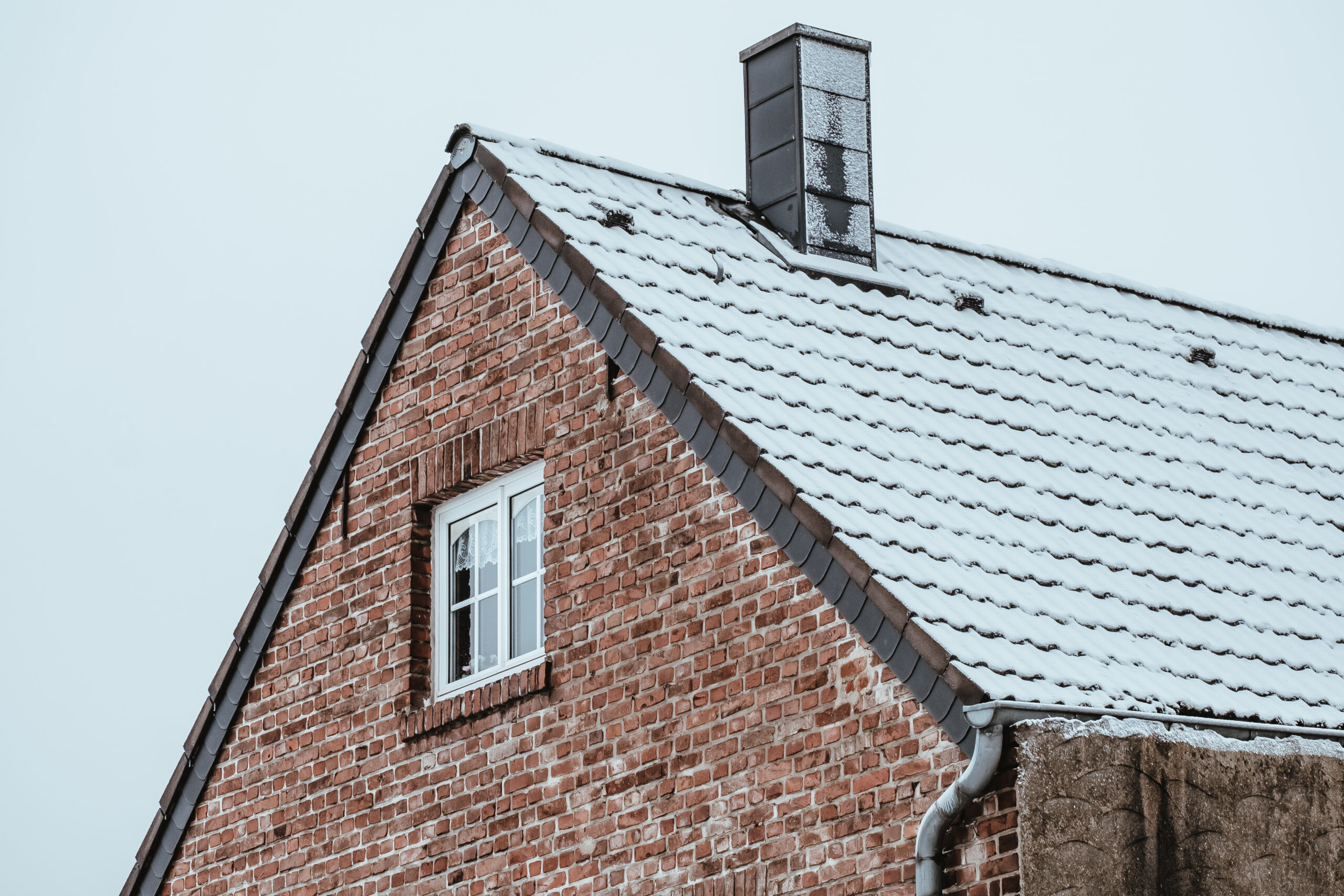
The Pointing Process:
- Removing Old Mortar: The deteriorated mortar is carefully removed from between the bricks or stones.
- Applying New Mortar: Fresh mortar is applied to the joints, matching the original as closely as possible.
- Finishing: The new joints are tooled to match the surrounding masonry, ensuring a consistent appearance.
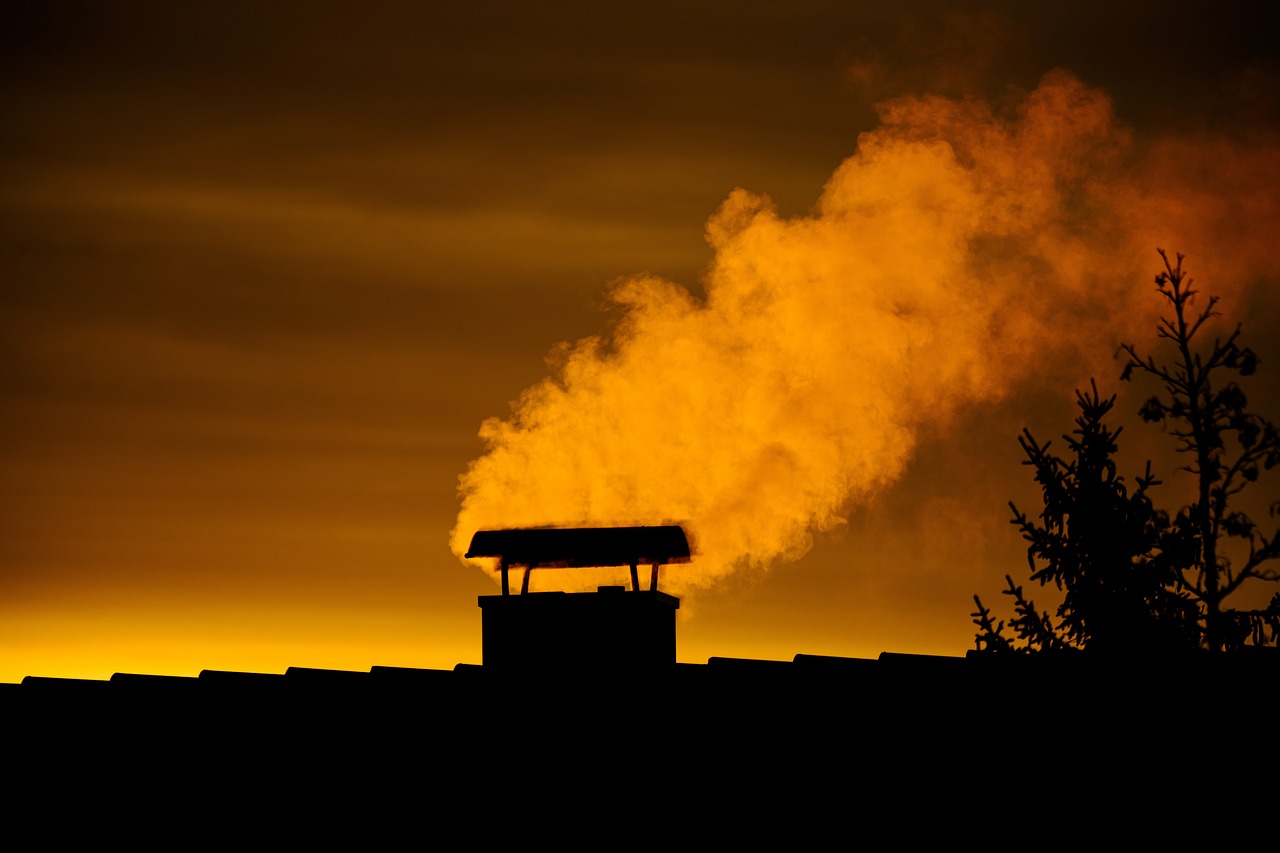
Rebuilding Process:
- Assessment: A thorough inspection determines the extent of the damage and the scope of the rebuild.
- Demolition: The damaged sections of the chimney are carefully dismantled.
- Reconstruction: Using new bricks and mortar, the chimney is rebuilt to its original specifications or improved upon.
- Finishing Touches: The rebuild is completed with proper flashing, capping, and waterproofing to ensure durability.
Chimney Rebuilding
In cases of severe damage, a complete or partial chimney rebuild may be necessary. This involves reconstructing the chimney from the roofline up or in some cases, from the foundation up.
When to Consider Rebuilding:
- Severe Structural Damage: Extensive cracks, leaning, or collapsed sections may require a rebuild.
- Fire Damage: Chimneys that have suffered from chimney fires often need to be rebuilt.
- Advanced Deterioration: When pointing and patch repairs are no longer sufficient, a rebuild may be the best solution.
Chimney Waterproofing
Waterproofing is a preventive measure designed to protect the chimney from water damage. While masonry is durable, it is also porous, allowing water to penetrate and cause deterioration over time.
Benefits of Waterproofing:
- Prevents Water Absorption: A waterproofing treatment creates a barrier that prevents water from being absorbed into the bricks or stones.
- Reduces Freeze-Thaw Damage: By preventing water ingress, waterproofing reduces the risk of damage from freeze-thaw cycles, where trapped water expands and contracts.
- Extends Chimney Life: Regular waterproofing can significantly extend the life of the chimney by preventing water-related damage.
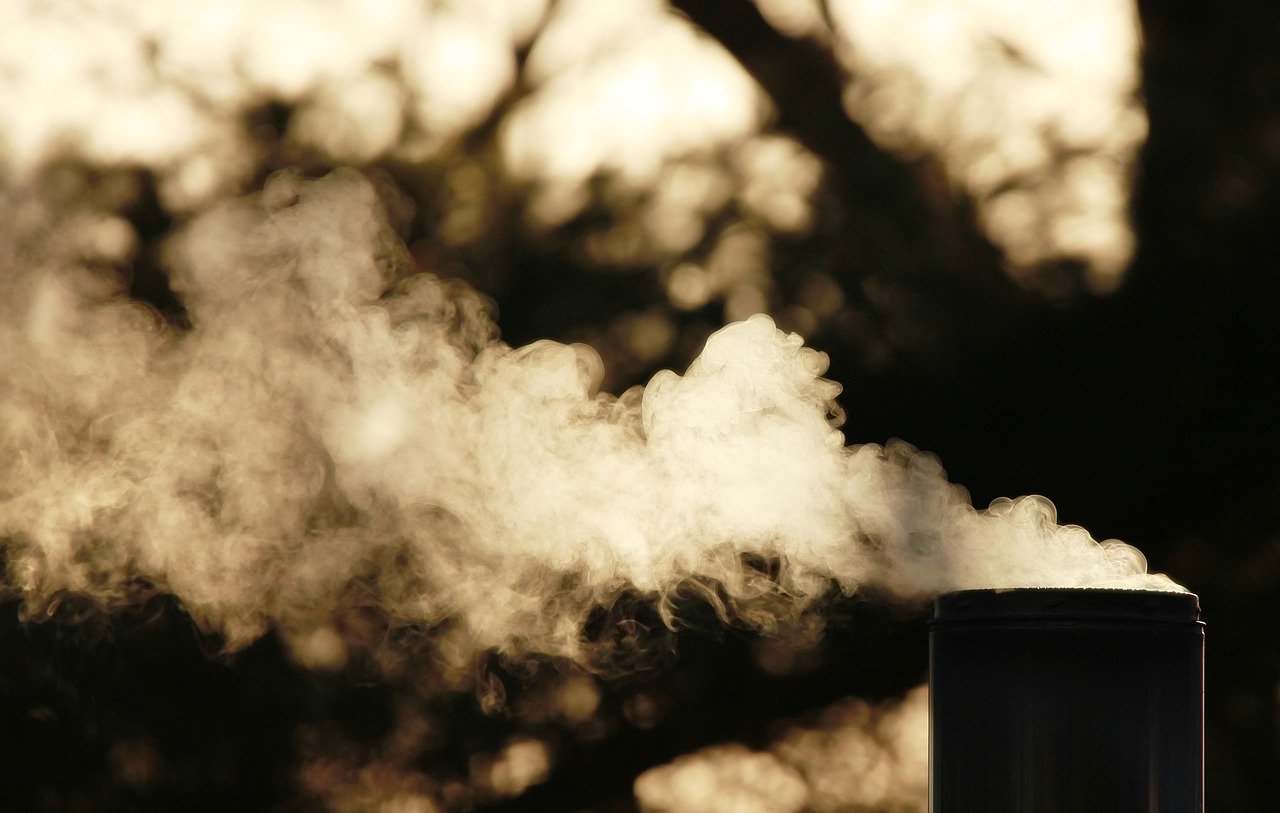
Waterproofing Application:
- Cleaning: The chimney surface is cleaned to remove dirt, mildew, and old sealant.
- Application: A waterproofing agent is applied evenly across the entire chimney surface.
- Curing: The treatment is left to cure, forming a protective barrier against water.
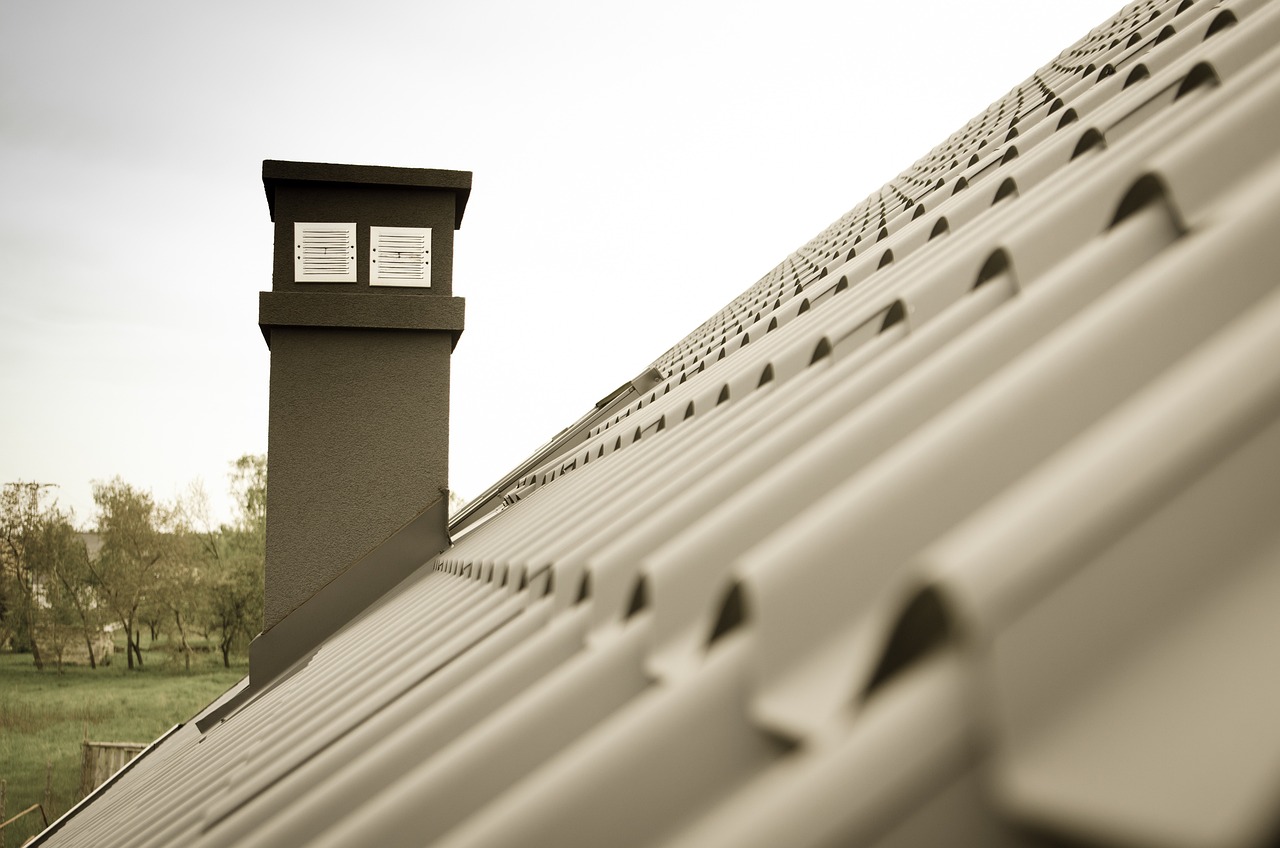
Repairing Flashing:
- Inspection: The flashing is inspected for signs of rust, gaps, or other damage.
- Replacement: Damaged flashing is removed and replaced with new metal flashing, properly sealed to the roof and chimney.
- Sealing: The edges of the flashing are sealed with a high-quality sealant to ensure a watertight barrier.
Flashing Repairs
Flashing is a critical component of the chimney system, providing a waterproof seal where the chimney meets the roof. Over time, flashing can deteriorate, leading to leaks.
Common Flashing Issues:
- Rust and Corrosion: Metal flashing can rust or corrode, compromising its ability to keep water out.
- Poor Installation: Flashing that was not properly installed can lead to gaps and leaks.
- Wear and Tear: Over time, flashing can crack, pull away from the chimney, or become damaged due to weather.
Firebox Repair
The firebox is the area within the fireplace where the fire burns. Over time, the high temperatures and corrosive byproducts of combustion can cause damage to the firebox.
Common Firebox Problems:
- Cracked or Deteriorated Bricks: The bricks lining the firebox can crack or deteriorate due to heat exposure.
- Mortar Erosion: The mortar between the bricks can erode, leading to gaps that allow heat to escape.
- Metal Firebox Damage: In prefabricated fireplaces, the metal firebox can warp or corrode.
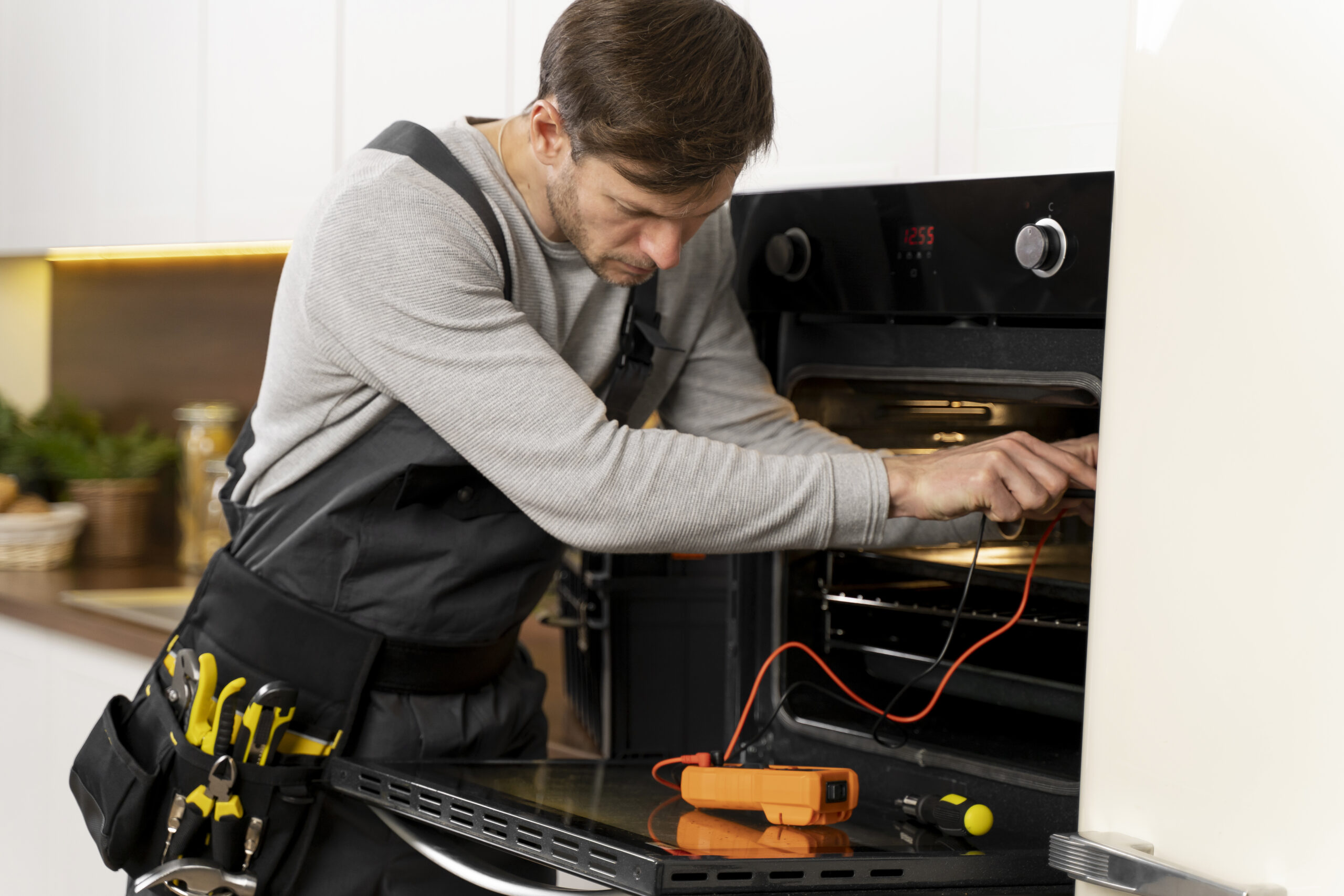
Firebox Repair Techniques:
- Tuckpointing: Eroded mortar is removed and replaced with new, heat-resistant mortar.
- Brick Replacement: Damaged bricks are removed and replaced with new firebricks.
- Refractory Panels: In some cases, refractory panels are used to line the firebox, providing a durable and heat-resistant surface.
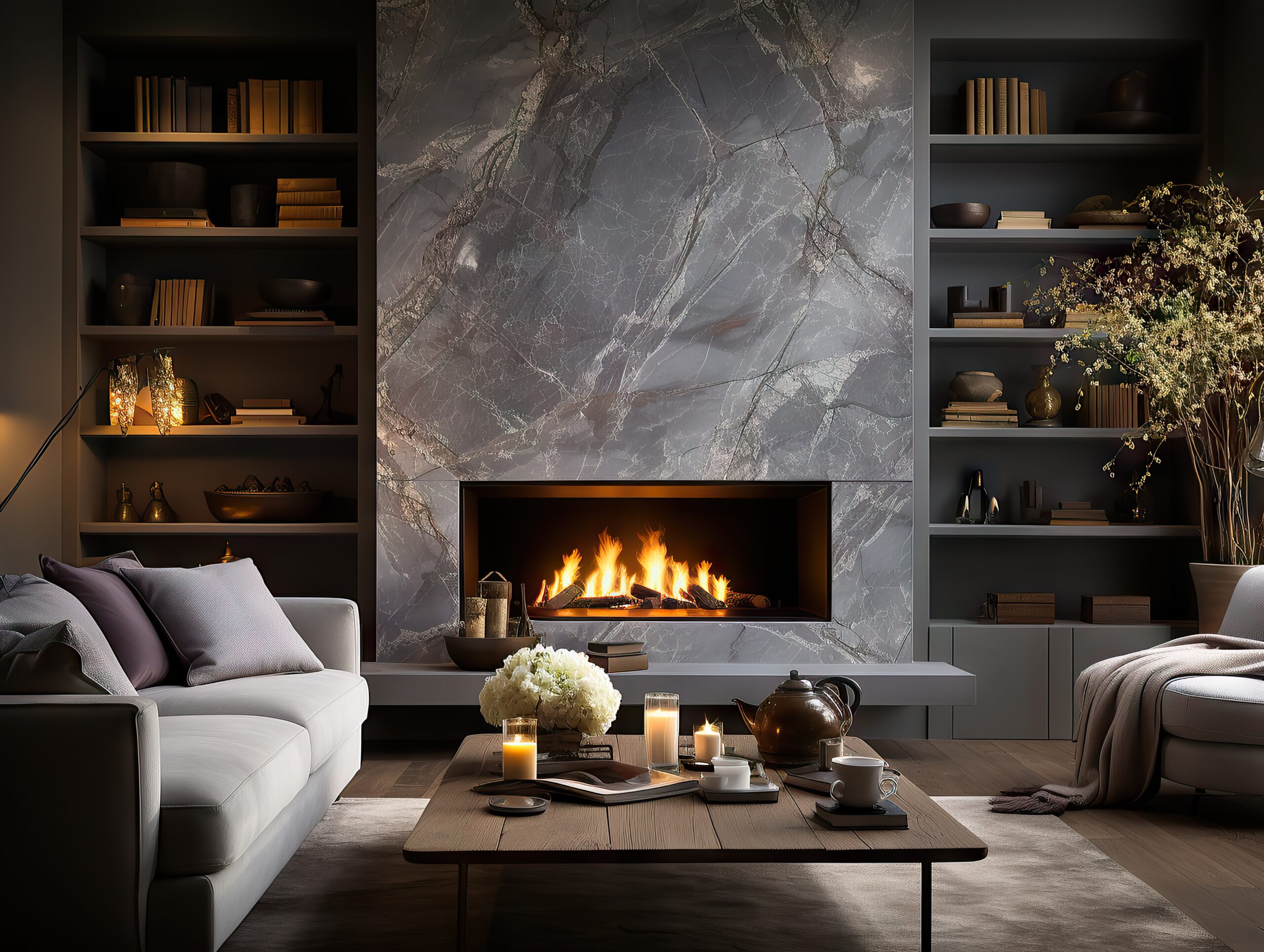
Solutions for Basement Fireplaces:
- Installing a Chimney Fan: A chimney fan can help improve draft in a basement fireplace.
- Waterproofing: Waterproofing the basement walls and fireplace structure can help prevent dampness and water damage.
- Inspection and Repair: Regular inspections of the foundation and chimney are essential to identify and address any structural issues.
Basement Fireplaces
Basement fireplaces present unique challenges due to their location below ground level. Issues such as poor drafting, dampness, and structural concerns are common.
Challenges with Basement Fireplaces:
- Drafting Issues: Basement fireplaces often struggle with drafting due to their low position relative to the rest of the house.
- Dampness: Basements are prone to dampness, which can affect the fireplace and chimney.
- Structural Concerns: The foundation and walls of a basement fireplace must be carefully inspected for signs of water damage or instability.
Chimney Liners
A chimney liner is an essential component of the chimney system, providing a protective barrier between the flue gases and the chimney walls. There are different types of chimney liners, including clay tile, metal, and cast-in-place liners.
Importance of Chimney Liners:
- Protecting the Chimney: A liner prevents the chimney walls from being exposed to corrosive byproducts of combustion.
- Improving Efficiency: A properly sized liner can improve the efficiency of the fireplace or stove.
- Preventing Carbon Monoxide Leaks: A chimney liner helps contain and safely vent carbon monoxide and other dangerous gases.
Liner Installation and Repair:
- Inspection: A thorough inspection determines the condition of the existing liner and whether it needs repair or replacement.
- Installation: Depending on the type of liner, installation methods vary, but all involve ensuring a snug fit and proper sealing.
- Maintenance: Regular inspections and cleaning are essential to maintain the liner’s integrity and performance.
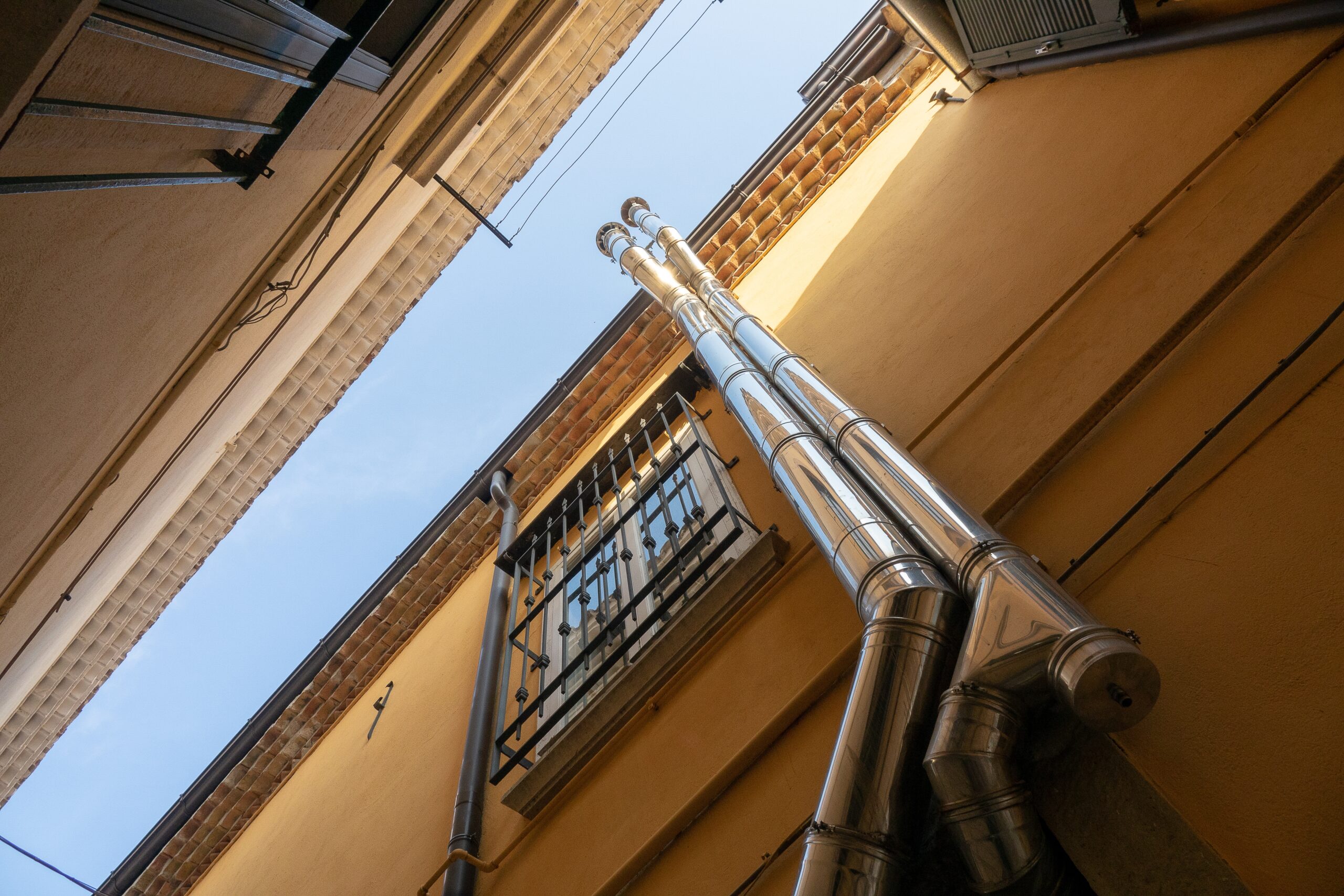
Types of Chimney Liners:
- Clay Tile Liners: Common in older homes, clay tile liners are durable but can crack over time.
- Metal Liners: Typically made of stainless steel, metal liners are often used in retrofits and are resistant to heat and corrosion.
- Cast-in-Place Liners: These liners are created by pouring a cement-like mixture into the chimney, forming a smooth, seamless lining.
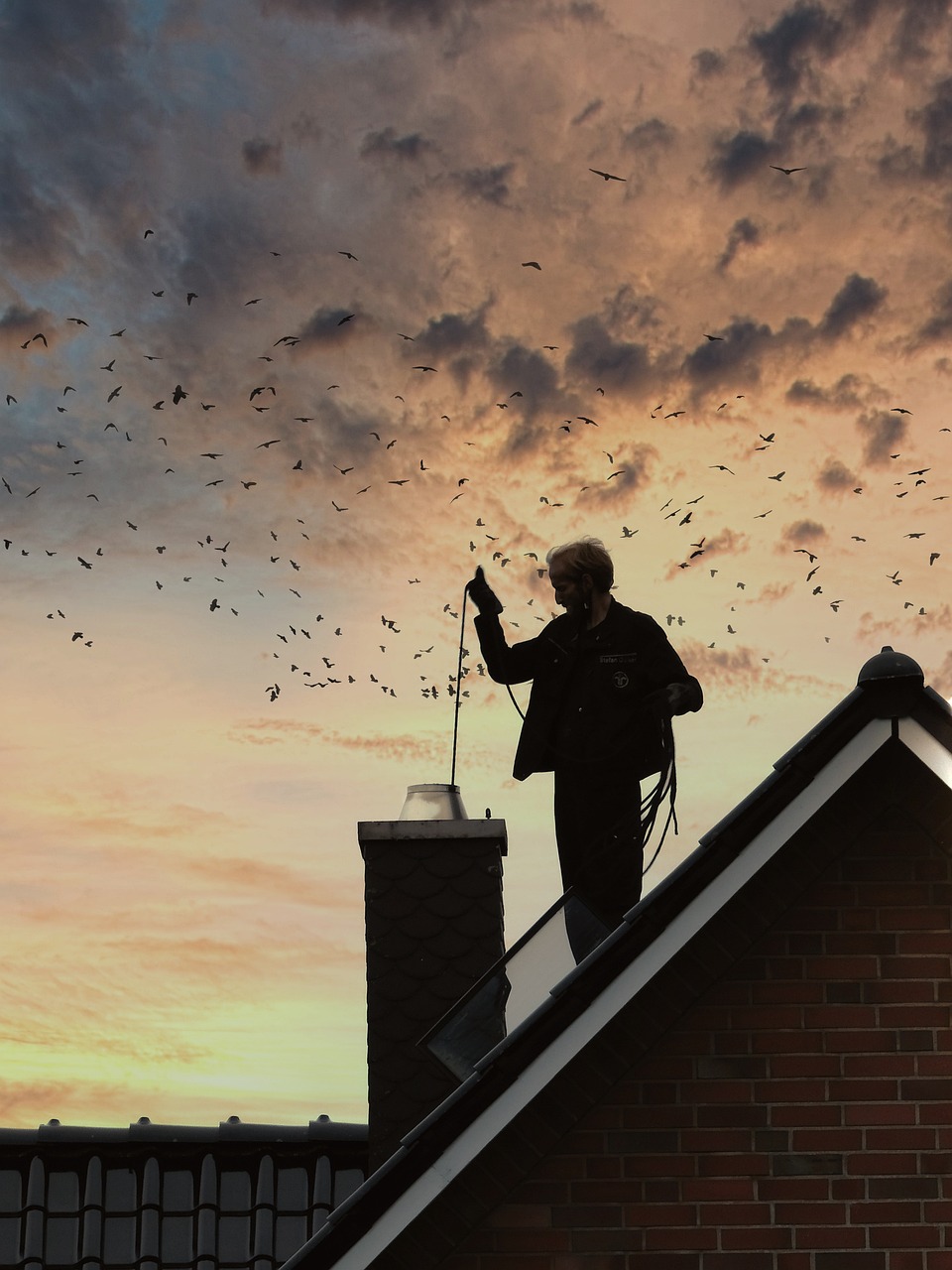
Types of Chimney Caps:
- Single-Flue Caps: These caps cover one flue and are typically made of stainless steel or copper.
- Multi-Flue Caps: Designed to cover multiple flues, these caps provide comprehensive protection for complex chimney systems.
- Custom Caps: For unique chimney shapes or aesthetic preferences, custom caps can be designed to fit and complement the chimney’s architecture.
Chimney Caps
A chimney cap is a protective cover that sits atop the chimney, preventing debris, animals, and rain from entering the flue. Chimney caps also play a role in improving draft and reducing downdrafts.
Benefits of Chimney Caps:
- Preventing Debris and Animal Entry: A cap keeps out leaves, twigs, and animals that can cause blockages.
- Reducing Water Damage: By keeping rain out, a chimney cap helps prevent water damage to the flue and chimney structure.
- Improving Draft: Some caps are designed to improve draft and reduce downdrafts, enhancing the fireplace’s performance.
Installation Process:
- Measurement: The chimney flue is measured to ensure the correct cap size.
- Attachment: The cap is securely attached to the top of the chimney, typically using screws or brackets.
- Inspection: A final inspection ensures that the cap is properly installed and functioning as intended.
Chimney Dampers
A chimney damper is a device located in the throat of the chimney, designed to close off the flue when the fireplace is not in use. Dampers play a crucial role in energy efficiency and preventing heat loss.
Why Chimney Dampers are Important:
- Energy Efficiency: A closed damper prevents warm air from escaping the home in winter and cool air from escaping in summer.
- Preventing Downdrafts: A damper helps reduce downdrafts, preventing cold air from entering the home through the chimney.
- Safety: Dampers also help prevent animals and debris from entering the chimney when it’s not in use.
Damper Maintenance and Repair:
- Inspection: Regular inspections ensure that the damper is opening and closing properly and that the seal is intact.
- Repair or Replacement: Damaged or worn dampers should be repaired or replaced to maintain energy efficiency and safety.
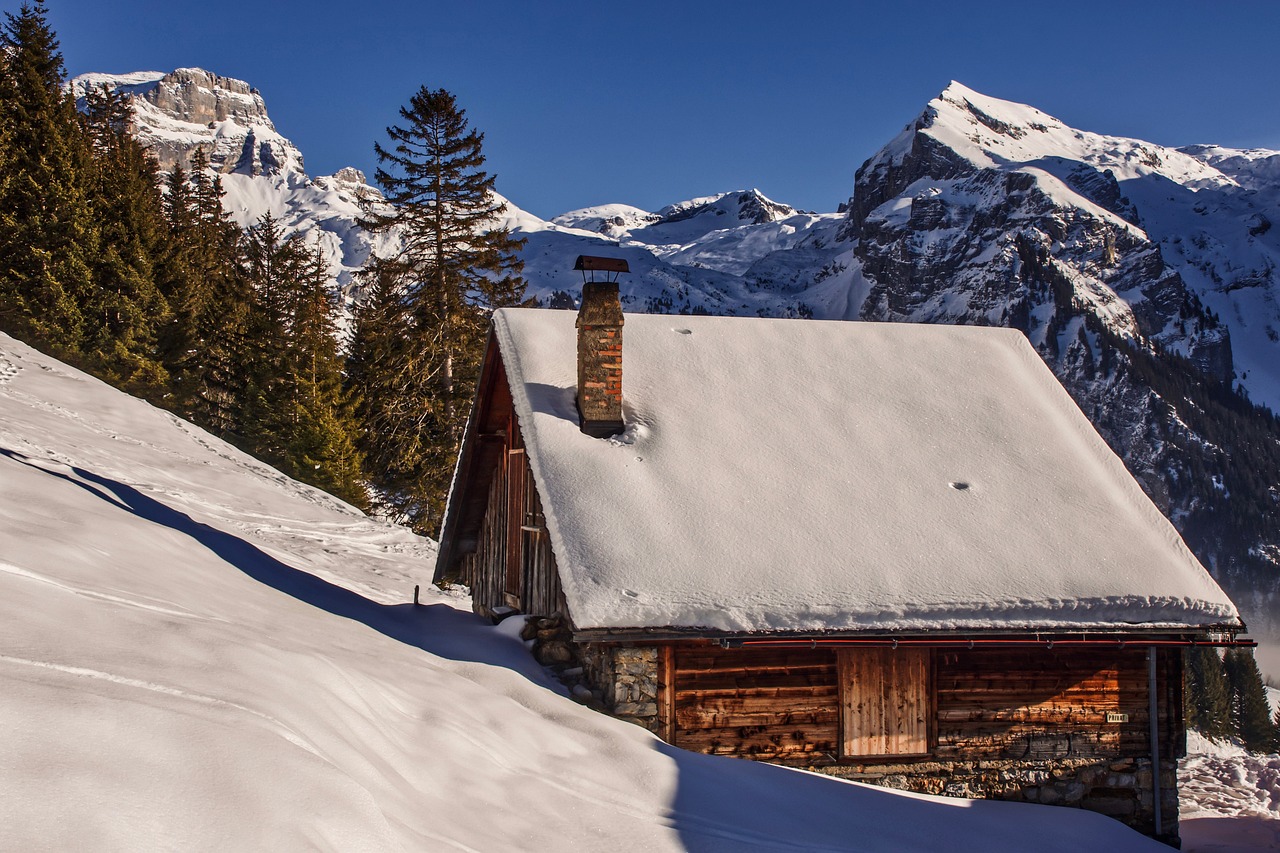
Types of Chimney Dampers:
- Throat Dampers: Located just above the firebox, these are the most common type of damper.
- Top-Sealing Dampers: Installed at the top of the chimney, these dampers provide an airtight seal and can also function as a chimney cap.
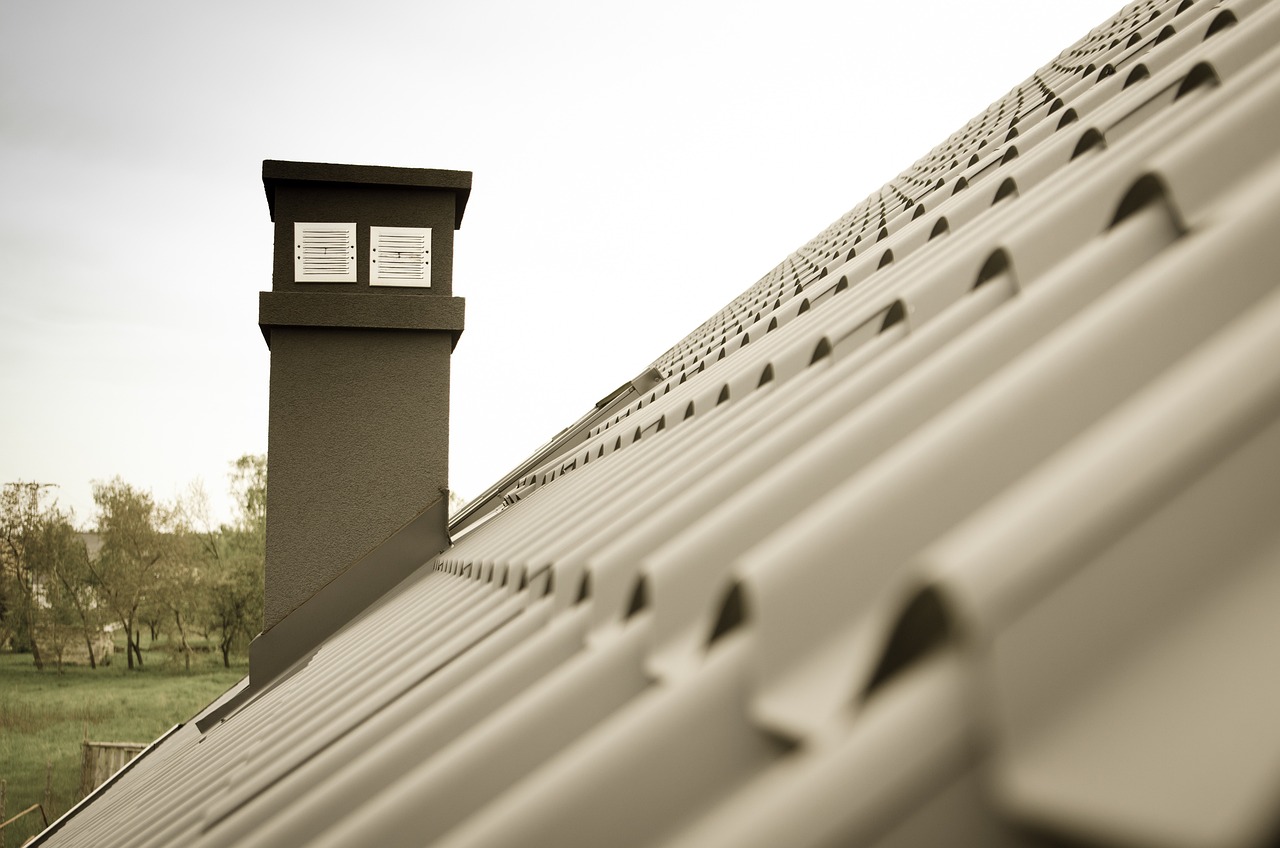
Replacement Process:
- Removal of Old Cover: The old, damaged chase cover is carefully removed.
- Installation of New Cover: A new chase cover is fitted and secured to the chimney chase, ensuring a watertight seal.
- Inspection: The installation is inspected to ensure that the cover is properly fitted and sealed.
Chase Covers
A chase cover is a metal cover that sits on top of a prefabricated chimney or chase, preventing water and debris from entering. Over time, chase covers can rust or corrode, leading to leaks and damage.
Importance of Chase Covers:
- Preventing Water Damage: A properly installed chase cover prevents rain, snow, and debris from entering the chimney.
- Protecting the Chimney Structure: By keeping water out, chase covers help protect the chimney and chase from rust, corrosion, and rot.
Types of Chase Covers:
- Galvanized Steel: Affordable but prone to rusting over time.
- Stainless Steel: Durable and resistant to corrosion, stainless steel is a long-lasting option.
- Copper: A more expensive option, copper chase covers offer excellent durability and a unique aesthetic.
Chimney Removal
In some cases, it may be necessary to remove a chimney entirely. This can be due to structural issues, a change in the home’s heating system, or aesthetic reasons.
Reasons for Chimney Removal:
- Structural Concerns: If a chimney is severely damaged or leaning, removal may be safer than repair.
- Heating System Changes: Homes that switch to central heating may no longer need a chimney.
- Aesthetic Changes: Some homeowners choose to remove a chimney to change the look of their home or to reclaim interior space.
Chimney Removal Process:
- Planning: The removal process is carefully planned to ensure that it does not affect the structural integrity of the home.
- Demolition: The chimney is dismantled from the top down, with bricks and debris carefully removed.
- Roof Repair: Once the chimney is removed, the roof is repaired and sealed where the chimney once was.
- Interior Repairs: Inside the home, the space where the chimney passed through may need to be patched, sealed, and finished to match the surrounding walls.
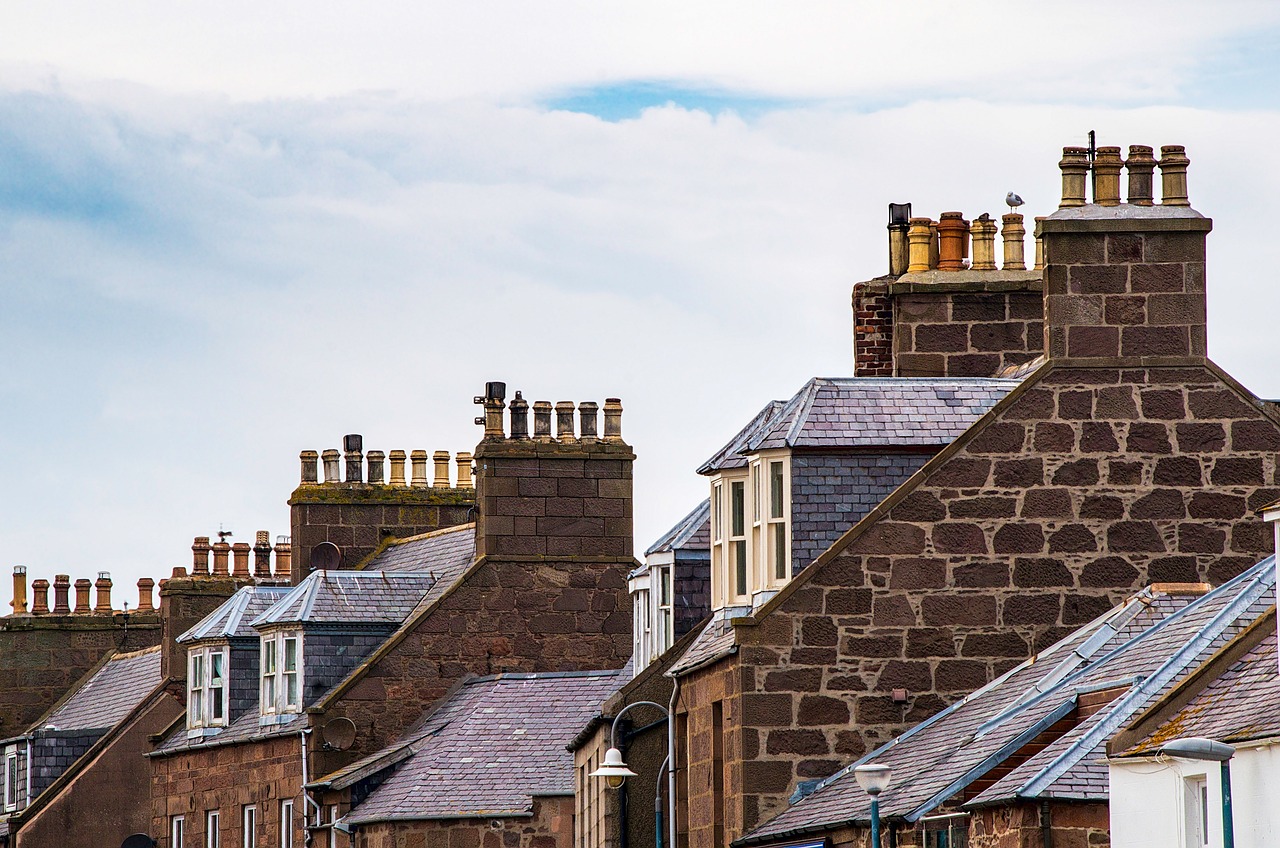
This comprehensive guide covers each aspect of chimney maintenance and repair, offering insights into why each service is essential, how it’s performed, and the benefits it brings to homeowners. Ensuring that your chimney is well-maintained not only enhances the safety and efficiency of your fireplace but also extends the lifespan of the chimney itself.
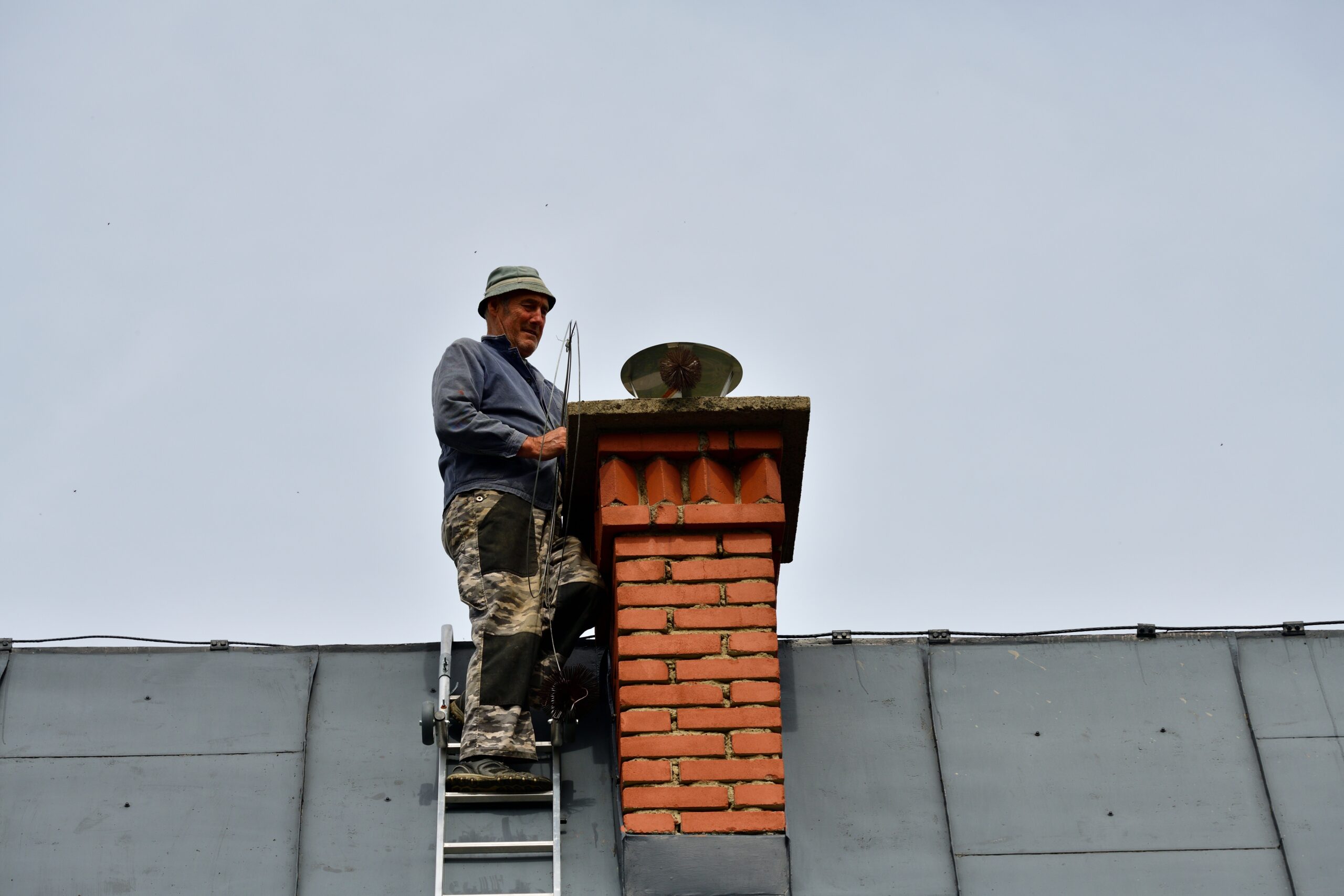
Sweeping as Part of Regular Maintenance:
- Fire Safety: Regular sweeping removes creosote, a highly flammable substance that can accumulate in the flue, reducing the risk of chimney fires.
- Improved Efficiency: A clean chimney drafts better, improving the efficiency of your fireplace or wood stove.
- Prevention of Obstructions: Sweeping also removes any obstructions such as bird nests, leaves, or other debris that could block the chimney and cause smoke to back up into the home.
Together, Chimney Inspection & Sweeping play a crucial role in ensuring the long-term safety, efficiency, and performance of your chimney, providing a safe environment for your home.
Chimney Inspection & Sweeping
Chimney Inspection and Sweeping are the first lines of defense in maintaining a safe and functional chimney. Regular inspections help identify potential issues before they become serious problems, while sweeping ensures that the chimney remains free of hazardous blockages and buildup.
Importance of Chimney Inspection:
- Early Detection of Issues: Regular inspections can reveal cracks, blockages, or structural damage that, if left unchecked, could lead to fires or other hazards.
- Compliance with Safety Standards: An inspection ensures that your chimney meets all current safety standards, which is particularly important if you are buying or selling a home.
- Peace of Mind: Knowing that your chimney is in good working order provides peace of mind for homeowners who rely on their fireplace for heat.
Inspection and Sweeping Frequency:
- Annual Inspections: It is recommended to have your chimney inspected at least once a year, even if it is not used frequently.
- Sweeping as Needed: The frequency of sweeping depends on how often the fireplace is used, but it is typically needed at least once a year for most households.